All Leathered Up
Leather: where to get it? I needed a high quality, smooth calf leather that I could turn into Russian Calf. Juliayn Coleman, conservator, design bookbinder, teacher, and avid cyclist – bicycles, that is ;-) was kind enough to take my call. In addition to all that, she's currently the president of the Hand Bookbinders of California.
Juliayn is always on board for my weird questions or requests, and invited me to Book Island, and her Oakland Studio. I bought a portion of an undyed Hewit archival repair calf skin. Once the transactional aspect was concluded, we did a little bookbinding gossip, came up with some ideas for HBC events, classes, etc., and I was on my way.
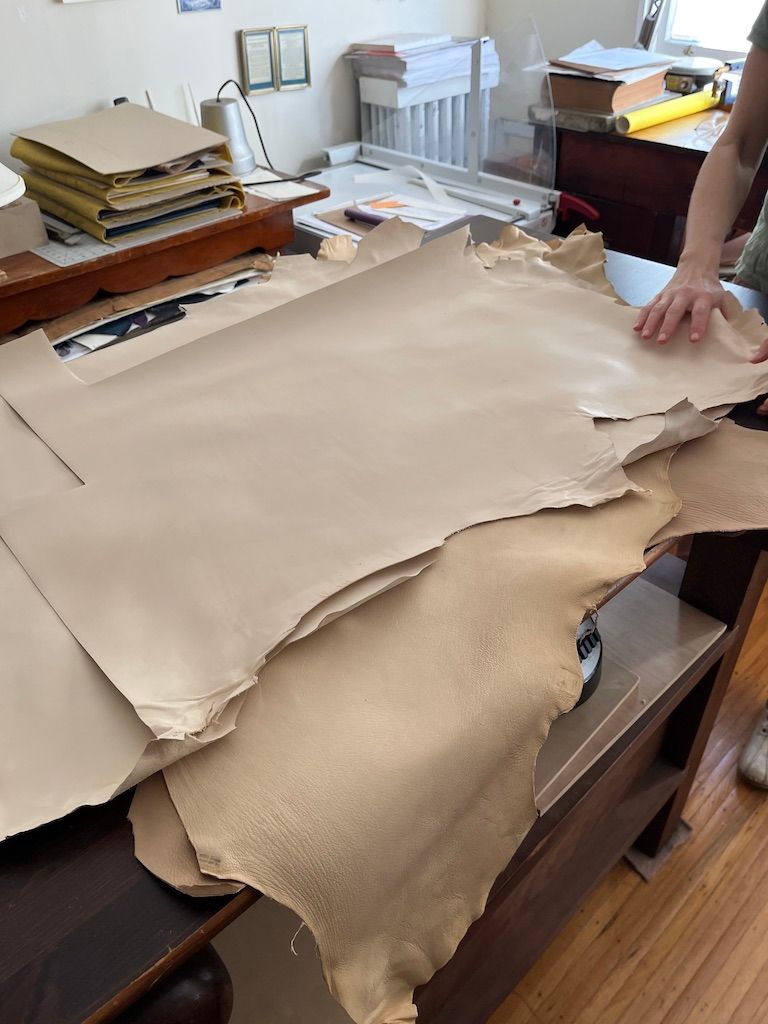
The concept is to make a Russian Calf with the traditional chevron pattern. I was asked by Michael Anthony Carnacchi about its use as a bookbinding leather back in 2009. He was researching Abraham Lincoln's boots and was making a replica pair. I'd learned a lot about tanning skins when I researched parchment recipes in the 80's, so I did some research. At the time, I couldn't find any leather manufacturer who was reproducing this birch bark oil-treated leather. We spent a few weeks searching, calling leather manufacturers (yes, we did talk with the Meyers at Pergamena, but they weren't interested in the project).
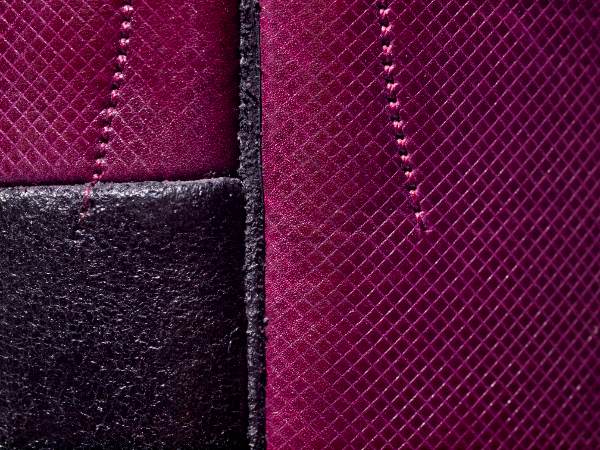
I've been picking away at this post for a few weeks now because I wanted to be able to write a little more than the paragraph above. This time around I found that a British leather manufacturer does make something, but the somewhat random pattern found in modern reproduction Russian Calf (see below) doesn't have the clearly delineated chevron pattern associated with it found in books from the 18th and 19th centuries. They've designed in imperfections in the pattern to emulate a poor roll technique, but to my mind it looks more like a momigami than a carefully patterned leather.
What really surprised me is that I found a 2012 article by Valeria Tsygankova about Russia Calf. I've spent the morning reading, and further researching the author, the article, and am ready to publish this post as my frustration at how some institutions build their downloadeable articles baffles me. In addition to the article, there's a translation of a recipe from 1807 translation. This one doesn't give the translator's name, where it was found, or much of anything beyond the recipe. I'm moving ahead as it's not that important. But the recipe is important to me because I'm using it to recreate the Russian Calf. It calls for an alum-tawing rinse after the oil infusion. I'll give that a try (and report later!)
You might be wondering if I'm not following the printer's dictum: Stop! Think! There must be a harder way! You might be right, but in my defense, it's not necessarily harder, just a little more labor to get it right. I'm always up for following old recipes as a way to learn from the past, by emulating it.
I acquired some birch bark oil (support your local herbal store!) and wanted to test how easy it would be to get the oil into the flesh side of this leather without soaking through to the front. It turns out that it's not that easy, so I'm still experimenting with how to apply it. Dry leather is thirsty. That's what you see in the first photo - the oil has to be applied thick to penetrate evenly but it penetrated to the front.
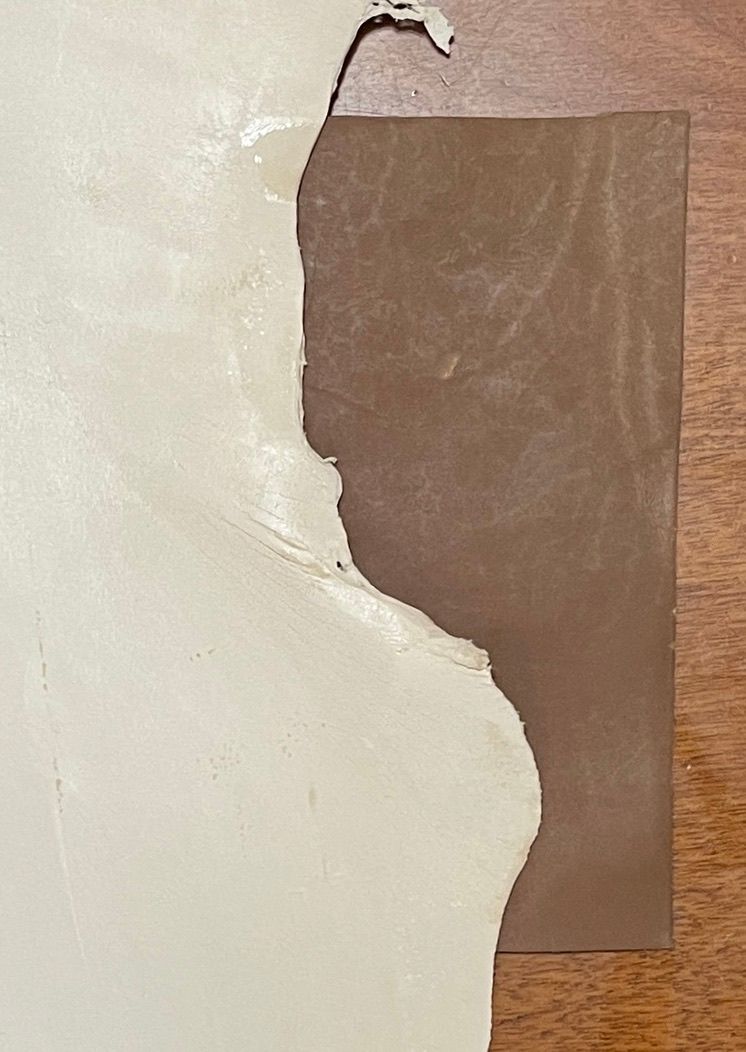
It took me a little while to realize that applying oil is the same as getting ready to tool or mould the leather. It's got to be damp – not sopping wet. To get that without staining, the whole surface has to be dampened. Below you see dampening on the front of the leather, and on the back of the leather on the right. Each piece was then oiled with a damp rag and a number of drops of birch bark oil. The color variation isn't quite accurate, but it's close enough to see that there's a slight darkening when the moisture is applied to the back.
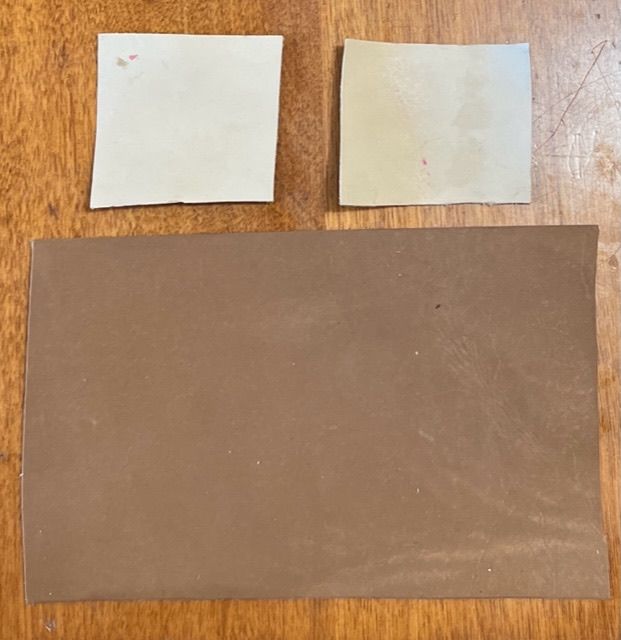
After oiling, I'll dye the leather, perhaps with cochineal (a dye made from the bodies of little red bugs.) Once I lace the quarter-sawn oak boards onto the textblock, I'll stamp the leather with a Russian Calf pattern on the front and back panels, and tool the plain leather over the cords.
To finish off the binding concept: I may etch a thin-gauge metal panel for the front which will key into the stock certificate blank endpapers. A story of Wall Street demands nothing less!